Share
Pin
Tweet
Send
Share
Send

Near the summer cottages there are often shallow ponds, but it is difficult to take water from them with a bucket: you have to walk along the bottom, dirt rises when typing, the water is very muddy. There is a simple way out of the situation - to make an elementary submersible pump with a centrifugal impeller. The height of the water rise is within 2-3 meters, which is enough for domestic needs.

Tools and materials
Prepare two electric motors for 12 V, you can take from car wipers (or buy one powerful motor on Ali Express) Pieces of plastic pipes of various diameters, sizes are selected taking into account the parameters of electric motors. We need epoxy glue and cold welding, a grinder, a drill with a set of drills, a strip of galvanized sheet steel, a piece of even plastic, a bend for pipes and a flexible hose. You will need a wire with a diameter of 0.5 mm, a cable with a switch, for power you need to have a 12V battery, you can from a motorcycle. Couplings are made from an old telescopic antenna from the receiver, a wire is needed to support the axis. Sheet steel is cut with scissors for metal.
Manufacturing technology

Saw a piece of about 2-3 cm from the antenna, the diameter should be slightly less than the diameter of the rotor shaft.

Connect the two motors, pull the clutch onto the front end of the rotor of the first and the rear end of the second. Motors must be perfectly aligned, check this by rotating the shaft manually.


In this position, apply epoxy glue to the surface of the engines and attach the wooden planks. They require at least two pieces, only this amount will provide the necessary reliability.

After the glue has dried, solder the power cables to the motor outputs, the connections should only be parallel. The cable length corresponds to the distance from the immersion of the pump to the location of the battery. Observe polarity, insulate adhesions.

Place the prepared motors in a plastic pipe. Its diameter and length should ensure their free placement. To fix the elements in the pipe, pre-wrap strips of cold welding around the perimeter of each engine. Make sure that the rotor shaft is located in the center of the pipe and is strictly along its axis.

Carefully seal the front of the pump with cold welding, only the rotating shaft should remain open.



Impeller manufacturing
Cut out a circle from galvanized steel, find its center and drill a hole. The diameter should correspond to the diameter of the axis of rotation.


With metal scissors, cut four rectangles for the pump blades. Glue them upright to the circle. Make sure that all elements are arranged strictly vertically.

Prepare a second circle of sheet steel, drill a hole. Now its diameter is larger, within two centimeters. Water will be absorbed through it.
Spread with epoxy and glue to it the first part of the impeller with blades. All planes should be at an angle of 90 degrees, circles parallel.
Install a wire support element at the output. It should be bent with a ring, legs should be made at the ends to improve the fastening strength. Glue them, while remember to observe alignment.


Insert the metal axis into the impeller holes, glue it on both sides.

Slip the coupling from the antenna onto the axis and connect it to the motor shaft.
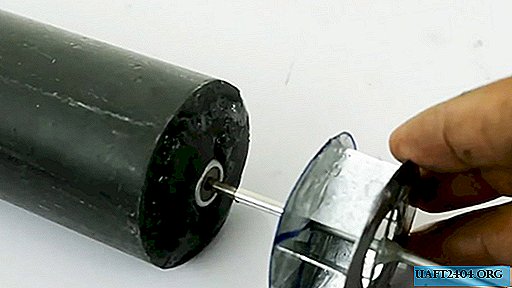
Manufacturing pump housing

Cut a piece of plastic pipe, select the dimensions according to the diameter of the wheel and its distance from the pipe with the engines.

Glue it to the plastic circle, make sure that the parts are perpendicular.

Make a hole with a pen drill. Its diameter should be the same as the inlet on the pump wheel.
Make a hole on the side of the impeller housing, the diameter is selected taking into account the size of the knee. To speed up the process, you can use an electric soldering iron.

Put a piece of plastic pipe about 3-4 cm long on the body. Its diameter of the passage should correspond to the outer diameter of the motor housing and go with a slight tension.

Insert the impeller with the motors into the casing, pre-coat the strip of cold welding around the circumference of the pipe. Adjust the position of the parts. In the center of the water inlet opening on the casing there should be the same device for supporting the impeller shaft as on the pump wheel. During rotation, it must rest in two places.


Attach the elbow to the water outlet from the body, the second hole is facing in the direction of the hose. Carefully process all the fittings with mastic.

Close the inlet of the pump casing with a suitable cover, glue it with epoxy glue.

Insert a flexible hose into the elbow, fasten and seal the entry point. Tie the hose to the body of the submersible pump, connect to the battery.


The product is ready for use, dip it in water and turn it on.


Make sure that the suction port is above the bottom of the pond and does not trap dirt.

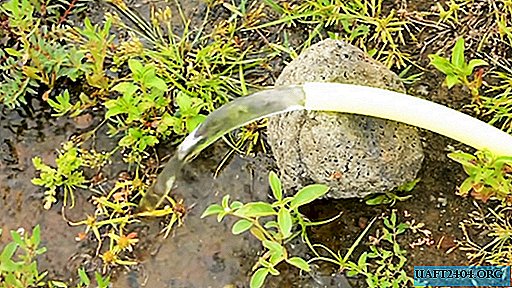

Conclusion
It is recommended to use the pump for a short time - the casing of automobile engines cannot protect for a long period of time from the ingress of water, it will get through the bearing of the rotor shaft. It is very difficult to find hermetic views with a housing of at least IP 67, and they are expensive.
Share
Pin
Tweet
Send
Share
Send